Cable bus and bus duct share certain similarities in system weight, power consumption, medium voltage drop, and enclosure size. However, they also have their differences that make electrical engineers favor one system over the other.
What is Cable Bus?
A cable bus is an electrical system that is made up of a ventilated metal casing that harbors fully insulated conductors that are suspended at specified cable spacing intervals. Unlike bus duct and cable tray, the metal cable bus housing is designed with cable support blocks that prevent short-circuiting and help to maintain cable spacing. This results in lower operation temperatures than conventional cable tray, conduit or bus duct.
Components are made of aluminum which is light-weight and highly resistant to corrosion and other environmental elements. The cable bus systems maximizes current ratings for each conductor.
View Our Modular Cable Bus Power Distribution System Products
What is Bus Duct or Bus Way
A bus duct, on the other hand, is an alternative means of conducting electricity made up of a sheet metal duct. This busway housing is constructed of a metal duct contains either aluminum or copper busbars that are designed to conduct a substantial current of electricity. They often have bolted bus joins or splices that can cause future failures.
Non-segregated phase bus runs are designed for use on circuits whose importance requires great reliability. Typical of such applications are the connections from transformers to switchgear assemblies in unit substations, connections from switchgear assemblies to rotating apparatus, and tie connections between switchgear assemblies.
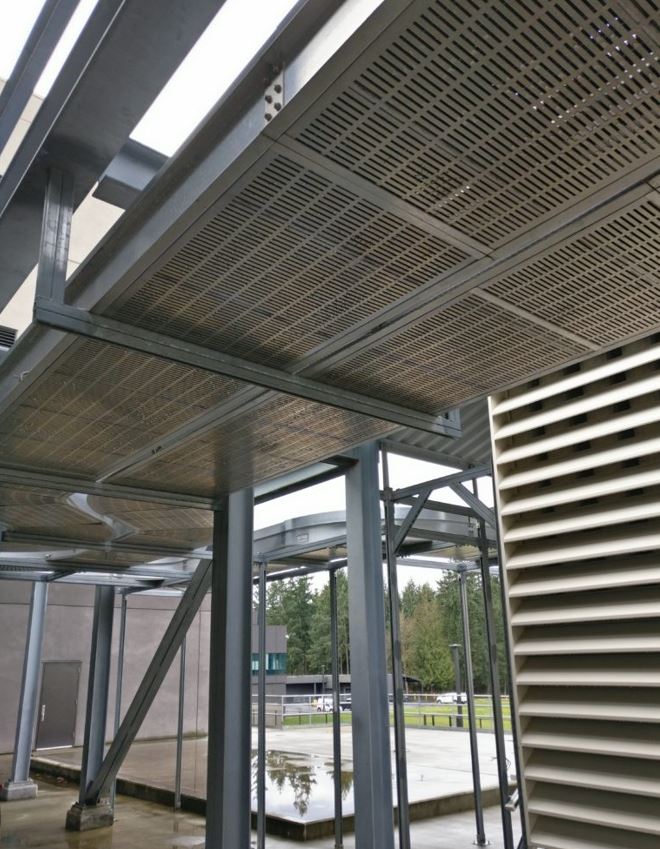
Non-segregated phase bus is an assembly of bus conductors with associated connections, joints and insulating supports confined within a metal enclosure without interphase barriers. The conductors are separated and insulated from each other and grounded by insulating bus supports.
This article discusses the differences between cable bus and bus ducts and which one is most preferred in electrical power distribution.
Flexibility
Distribution of electrical power takes precision. Cable bus systems can accommodate unforeseen differences between the engineered drawings and actual construction with little or no delay. It can be easily cut or adjusted. This is if a shorter bus length is required and comes with extra additional cables and housing. From conception through to final installation, each cable bus system is custom built to precise specifications. Components, including supports and brackets, are specially manufactured for each custom design. The flexible manufacturing process is able to deliver the specialized components required for every application.
The bus duct arrives as a complete system with factory-installed conductors ready for assembly. This makes it very difficult to make small adjustments in the field because it is made to the exact measurements as specified in the engineered drawings.
System Maintenance
The conductors of cable bus are fully continuous throughout the system, which helps to eliminate joint resistance and any other potential weaknesses. This helps reduce maintenance and operating costs largely. Busbar jointing is quite simple, as it requires the use of bolted connections. However, it requires regular inspections and adjustments due to increased joint resistance caused by inadequate conductor contact area. This drastically increases the costs associated with maintenance and operation.
Overall Installation Costs
A cable bus maintains a free air rating and greatly reduces the conductor materials costs as it only uses up to 40 percent less aluminum or copper. It does not require heavy lifting or special tools since the housing sections can be fitted easily to their designated spaces. This helps to reduce the labor costs and amount of time spent on installation. Each system is specifically measured, designed and manufactured for your project, eliminating the need for onsite adjustments and cutting. Custom installation drawings and step by step instructions provide a blueprint for positioning each piece during assembly.
A bus duct jointing on the other hand can be effective as it uses clamped joints or copper welding. However, the use of these extra materials to conduct electricity drastically increases the costs of materials and labor involved in the installation.
Fire and Safety Rating
Cable bus systems have a higher safety rating than bus duct or cable tray because of the high concentration of insulating materials that have been used in conductors and integrated cables. This makes it more efficient when it comes to dealing with fire as it has a high level of combustive energy. The combustive energy in bus duct is considerably lower because they do not have enough insulation like the cable bus. This means that the available insulation in bus ducts do not release enough toxic or corrosive gases in the event of a fire breakout.
Custom cable bus systems are designed to meet codes and standards for current ratings, voltage drop and installation requirements for the safety of the finished continuous energized system.
Service Life
The materials used in cable bus are made up of corrosion-resistant aluminum. Stainless steel hardware is also used in MDF systems to maximize its service life. In addition, the cables used in this electrical distribution system are suitable for both indoor and outdoor use. The enclosure of bus duct relies on being painted to prolong their service life and is merely plated steel hardware. Unlike the cable bus, bus duct and cable tray may require extensive maintenance to keep them in good condition for a long time.
Reliability
Reliability of these power distribution systems is paramount. A cable bus system is an end to end solution using continuous conductors eliminating the risk of failure inherent with multiple connection points. With no bus connections to fail, cables are braced and contained within the enclosure in the event of a short circuit or fault. A grounded metal enclosure, firestops, water tight equipment entry flanges and environmental seals ensure their long lasting integrity and peace of mind. Impervious to moisture and caustic materials in the surrounding environment. Naturally occurring condensation does not cause risks the way it does with traditional bus duct. This eliminates the need for cable bus systems to include expensive heaters or blowers that regulate bus duct systems.
Cable bus is more reliable than bus duct because it utilizes fully insulated power cables that are continuously connected from the source to the load. This eliminates intermediate splices allowing the connections to be done at the equipment terminals. On the contrary, bus duct have bar connections at every straight bus section and the end of the elbows and fittings. Over 90 percent of electrical failures arise from the number of connections connected from the source to the load. Since a cable bus minimizes the use of insulation splices and conductor connections, its system is substantially more reliable than the bus ducts.
Both cable bus and a bus way system have their benefits and downsides. However, the efficiency and effectiveness of a cable bus power distribution system far outweigh the benefits of a bus duct in several aspects as seen above. The choice between the two all comes down to individual preferences and what best suits the nature of the project.